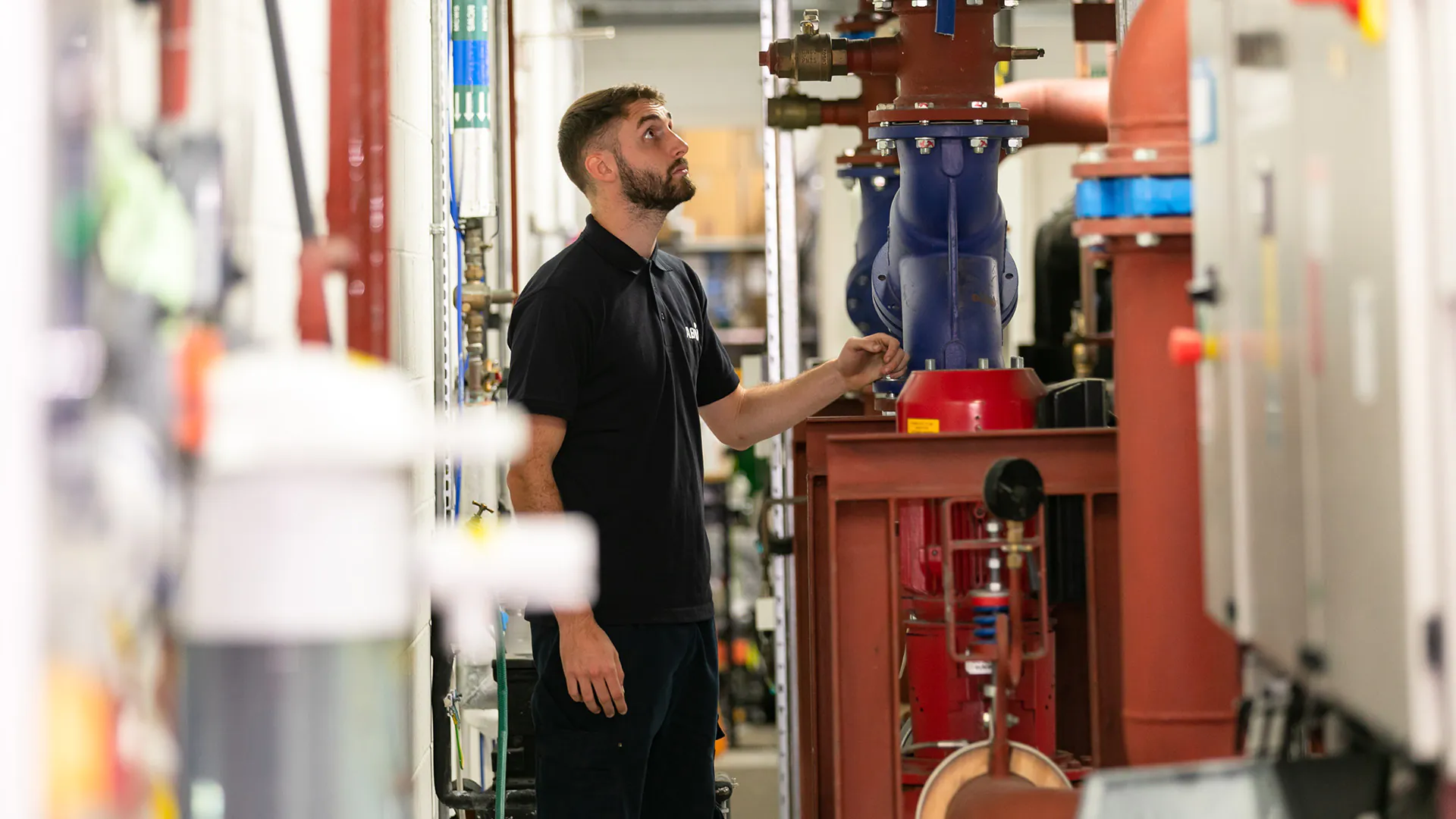
Challenge
The client, the largest indoor ski slope facility in Scotland, saw its backlog of technical engineering work grow significantly. As a public-facing business within the sports and entertainment sector, it was imperative that the client’s facilities remain up to industry standard, including HVAC asset installation, electrical power systems, and proactive maintenance capabilities.
As a result, the client required a supplier that could deliver consistently high standards across its entire technical operation. This included HVAC - with particular focus on ventilation and smoke extraction - electrical power, and a resident engineering team. The client also wanted to retain its reactive capabilities in the event of unscheduled downtime. Moreover, implementing a business management system (BMS), in the form of a computer-assisted facility management (CAFM) system, was identified as critical to track the site’s complex engineering operation.
“The client's public-facing facilities now have enhanced ventilation and safety controls, both for HVAC and secondary power operations.”
ABM was tasked with supplying an accredited engineering operation that could repair, maintain, and upgrade the client's mechanical and electrical infrastructure. This included its smoke extraction, fire prevention, and smoke control systems. ABM also needed to help ensure readiness and operability of the facility's secondary power supply for immediate activation.
Solution
ABM established a mobilisation plan that would guide operational implementation and subsequent service delivery. This was an essential first step, both in developing site knowledge and establishing a constructive client-supplier relationship.
Site tours and asset verification were critical in understanding the complexity of the client’s operation. The engineering team and supporting SMEs (subject matter experts) developed a routine PPM (planned preventative maintenance) plan to support service delivery and establish target KPIs to track.
This helped ABM understand which specialist suppliers would be the most beneficial for the client. As a result, the client deepened its resource pool and increased its budgetary efficiency through enhanced supply chains.
Moreover, this was key in identifying how ABM’s engineering teams could upgrade assets where necessary and begin planned maintenance services on the client's infrastructure. As a public-facing facility, ventilation, fire prevention, and smoke control systems were essential.
The assets and controls for these critical capabilities were quickly upgraded. For example, electrical teams installed new, more encompassing zonal panel control systems for smoke extraction across the site. This gave the client greater control over its internal systems and helps ensure greater safety for its customers.
Similarly, the client’s secondary power system was a necessity for long-term operational productivity and asset life cycles. In the event of unscheduled downtime, this electrical power system must immediately activate. To this end, ABM implemented Scotland’s first total shutdown on-site to test the client’s secondary power system’s integrity. Annual site shutdown tests are now part of the client’s routine maintenance.
Moreover, ABM and the client identified the need for a BMS system that could support on-site engineering work, both planned and reactive. This would enable greater client communication and increase efficiency through streamlined task management. Due to this additional BMS training for the engineering teams, the speed of reporting and communication has significantly increased. Similarly, it has given the client far greater strategic visibility over its operation, assisting both ABM and the client in identifying future opportunities for technical efficiency and productivity.
Benefits
- Operational integration: The client's technical operation is well-integrated, with a dedicated resident engineering team that provides regular service through both PPM and reactive maintenance.
- Accredited resident engineering operation: The client's HVAC and electrical operation is staffed by experienced and accredited engineers, including the City & Guilds (C&G) 2919 certification for EV installation and HV/LV (high voltage/low voltage) Authorised Person accreditation.
- HVAC and electrical maintenance: The client's technical operation continues to deliver specialised engineering and mechanical services and consistently meets target KPIs. Similarly, the client is well-positioned to enhance its complex electrical and ventilation capabilities.
- BMS training: The client’s complex technical requirements, which include substantial electrical and engineering work, are managed by a supporting CAFM system on-site. This has enabled greater productivity for the client, including additional management capabilities to organise resident engineering and specialist subcontractors alike.
- Effective PPM and reactive capabilities: The client’s smoke extraction and ventilation maintenance is conducted through PPM and reactive maintenance, ensuring the site can operate as needed for the public.
- Project management: The client continues to implement critical infrastructure projects alongside ABM. This includes multiple extractor installations, annual manual shutdown and secondary power integrity testing, and zonal smoke control panel installation.
- Enhanced supply chain: The client has access to ABM’s wider business network, including its specialised third-party suppliers. This has expanded the client’s capabilities, both in resources and budgetary efficiency.
- Critical safety infrastructure: The client’s fire prevention and secondary power supply are regularly tested and maintained, including power integrity testing to ensure compliance with safety regulations.
- Effective PPM system and reactive capabilities: The client’s technical operation continues to implement scheduled PPM timetables and reactive engineering works so that essential facility functions are in full working condition.
- Synchronised cause-and-effect system: The client’s projects, PPM scheduling, and reactive capabilities are supported by the site’s fully synchronised cause-and-effect system, meaning operational hazards and integration options are understood and risks reduced. As a result, the client’s operation now works with an in-depth knowledge of the site’s infrastructure.