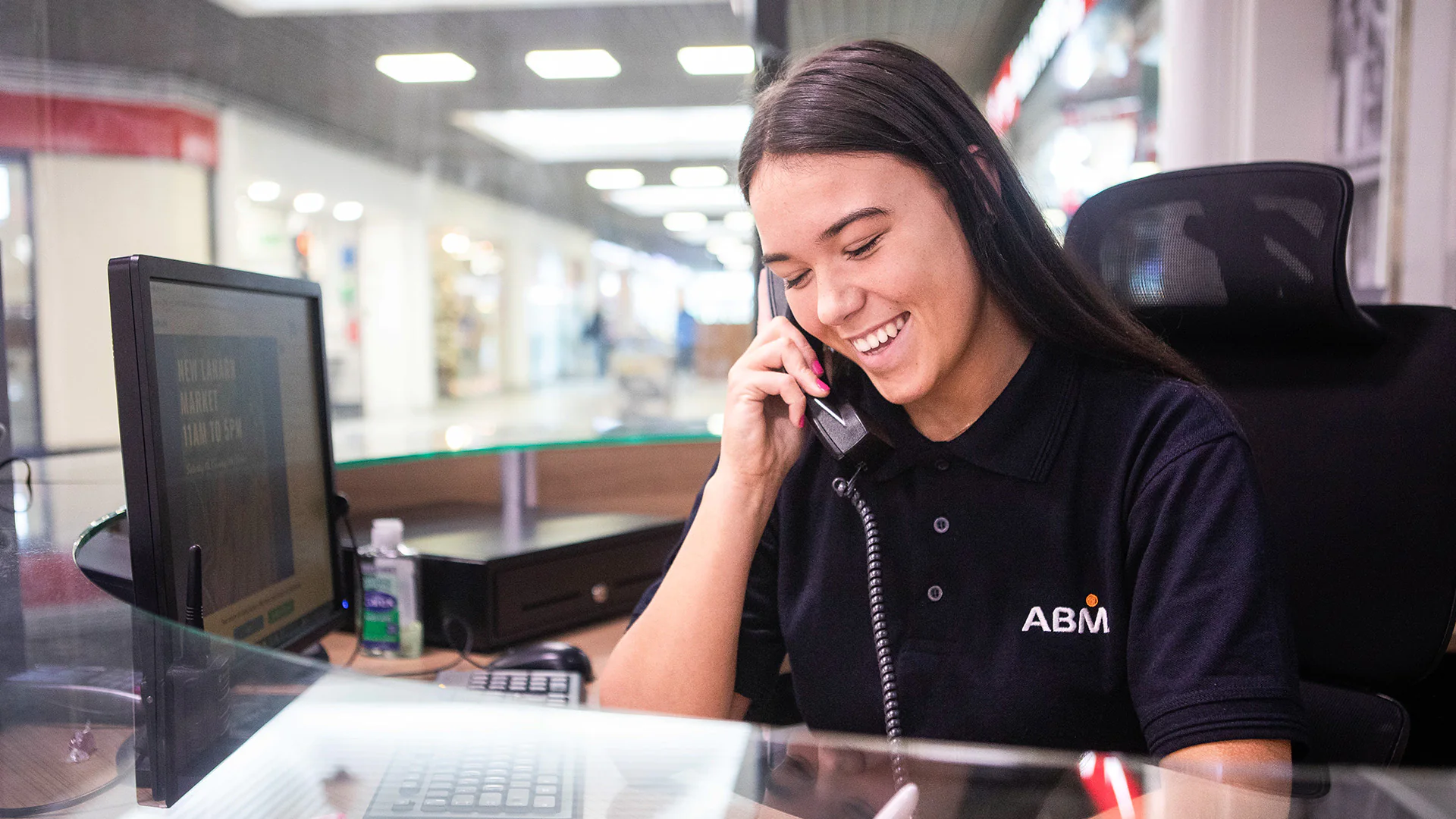
Challenge
Continuous improvement has become a core strategic focus for ABM, especially in delivering services for its clients. With over 1,600 clients across the UK&I, efficient and environmentally sustainable resource management was viewed as critical, both to support clients and site teams.
Many managers and client-facing subject matter experts (SMEs), for example, knew of valuable machinery, such as electric floor cleaners, that could be used productively at other locations. Yet such knowledge was often localized, and reallocating this equipment required extensive and time-consuming outreach. Additionally, ABM’s resource requirements for office and cleaning materials to engineering tools meant there was a surplus of unused equipment.
Solution
To address this, ABM created “The Stock Room,” a centralized digital hub listing all available equipment across the business. This hub aimed to reduce waste, improve cost-efficiency, support site teams, and implement sustainable resource allocation. ABM’s developers and business improvement experts decided to host The Stock Room on NucleusUK, ABM’s internal web portal for resources, workflows, operational support, and training.
Before the full launch, ABM’s Development and Business Improvement teams conducted trials to refine the application’s functions, involving stakeholders for insights into best practices, user experience, tracking, and inventory management. The Stock Room quickly became a valuable source of data, helping understand demand-based trends and accelerating mobilization timelines through optimized resource allocation.
Furthermore, ABM used The Stock Room to create a sustainable and cost-efficient closed-loop economy, allowing clients to utilize surplus equipment instead of purchasing new items. This circular economy sustained multiple projects and reduced waste streams.
Benefits
The Stock Room provided several benefits, including:
• Continuous Improvement: Enhanced tracking and logging support effective resource management and accelerated mobilization for clients. The data gathered also helped predict equipment demand.
• Cost Efficiency: Over £48,000 worth of machinery was redeployed through The Stock Room. For example, robotic floor cleaners valued at £5,000-£8,000 were allocated to different client locations.
• Streamlined Mobilization: The complexity of mobilization was reduced, offering visibility into available resources, including their quantity, service history, and location.
• Rapid Equipment Reallocation: Managers could quickly access The Stock Room, speeding up service delivery and project timelines.
• Single Point of Contact: The Stock Room acted as a centralized hub for clients and managers, reducing the need for external suppliers.
• Inventory Reporting: Managers could track inventories across ABM, supporting cost accountability.
• Enhanced Sustainability: The Stock Room helped reduce waste by allowing equipment to be offloaded and redeployed efficiently.
• Effective Resource Management: The platform enabled tracking from initial purchase to maintenance, ensuring quality.
• Future Functionality: The Stock Room’s tracking and measurement capabilities position it to develop additional client-benefiting features.
ABM’s Stock Room supported enhanced resource allocation for clients. Visit ABM.co.uk to learn more. © 2024 ABM Industries. All rights reserved.